How Ardagh Group Cut Their Audit Time By Four While Engaging More Employees In Continuous Improvement
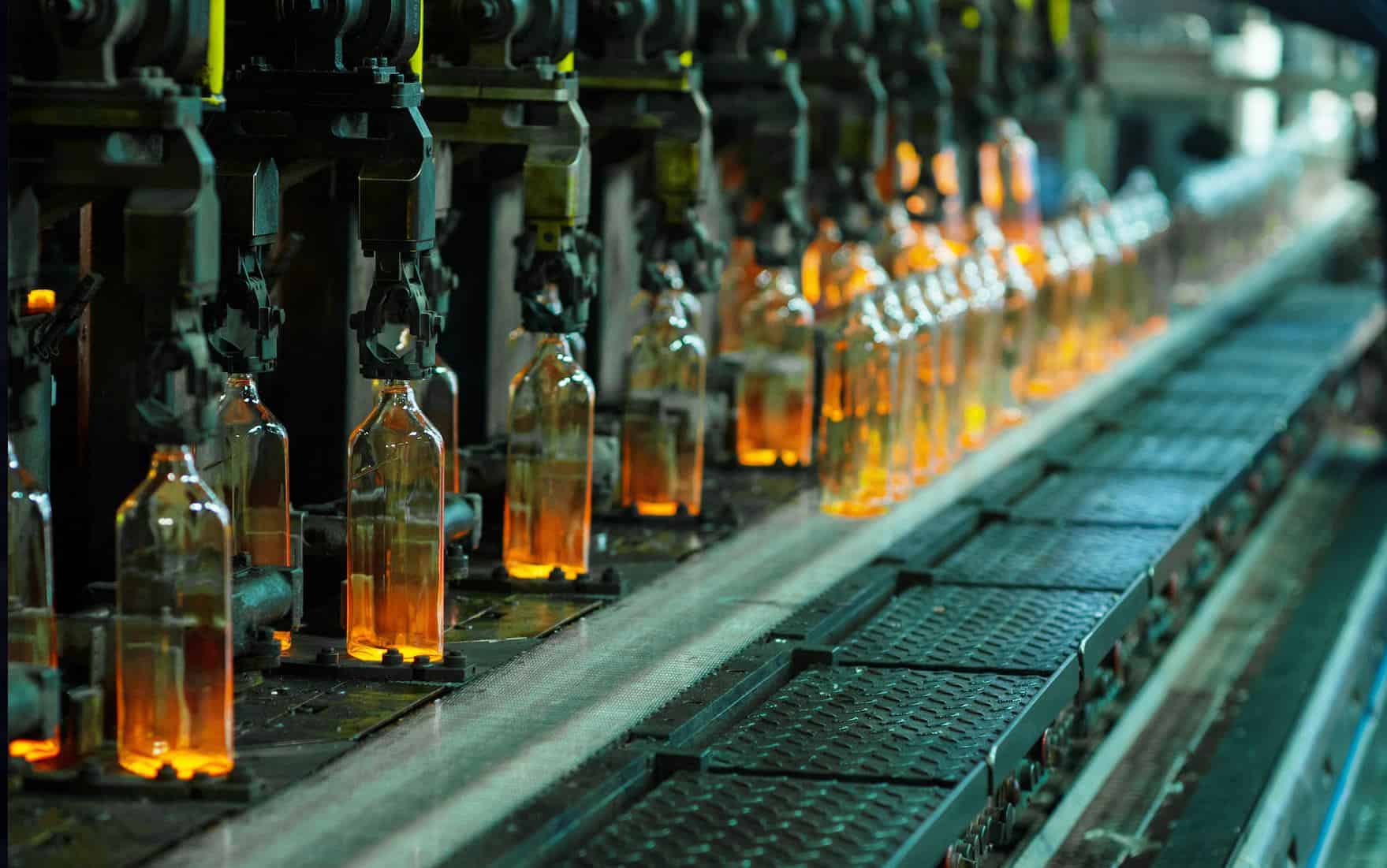
Ardagh Group is a leading supplier of sustainable packaging solutions, known for its focus on continuous improvement in all aspects of the business. The company has a global presence with 56 metal and glass production facilities in 12 countries, employing 16,000+ people.
Ten years ago, Ardagh Group started a Lean Six Sigma program to instill continuous improvement in their day-to-day work. Unfortunately, one critical challenge made monthly 5S erratic and uncoordinated — lack of time.
Manual data entry was eating up precious hours that some Health and Safety managers just didn’t have. Managing the initiative on a global scale was almost impossible because the entire LSS process was paper-based. There wasn’t a centralized system.
To get a better idea of the unique LSS challenges that the company faced, we interviewed Pierre Autret, the director of Lean Six Sigma at Ardagh Group.
The administrative nightmare
In a large global organization, it’s natural to see some level of disparity between units. This was the case with Ardagh Group. Some of the plants had an extremely meticulous and structured approach to LSS audits, following instructions to the T. This was great on one hand but also meant a lot of wasted time in administrative work. Others postponed these audits in favor of more urgent tasks.
Mr. Autret noticed that more and more plants started pushing LSS audits to the backburner. In many cases, the audits were not performed or not well-documented.
“The average time we were spending on this audit was at least 10 people per plant, spending 2-3 hours per month to go through all the audits.
And why?
Because it was mainly Excel-based and, so, all the questions were in Excel. It was extremely not standardized across plants, regions, and worldwide.”
Each auditor was going on the shop floor with a print of the master Excel checklist, taking notes and pictures. Then they went back to the office to spend hours documenting their observations. The process was time-consuming and ineffective, slowing down continuous improvement throughout the organization.
The low engagement levels
The Ardagh vision is that everyone can be a process improver, every day. From the shop level all the way to upper management.
“Our vision is to have everyone a process improver every day in our business and therefore what we are looking at is how can we engage people who are coming [from] 8-hour shifts, potentially doing repetitive tasks; [to give them] a voice to show that they care about the environment, they can submit suggestions, they can validate that everything is in place.”
But it’s difficult to engage people in something they don’t understand, especially if requires a lot of effort to do. That was exactly the challenge the company’s LSS initiative was facing and it was a natural consequence of the high administrative burden.
“Most of the management is 100% onboard [with LSS], educated, trained, and certified but we don’t have everyone. We still have a lot of people in our plants who, sometimes, will have no idea of what all of this is about.”
Watch our interview with Pierre Autret, the director of Lean Six Sigma at Ardagh Group
One Dutch plant lead the change
During a visit to the Ardagh Dongen plant, Mr. Autret found that they were trying out Capptions. The facility’s safety leaders showed him how they used Capptions to perform 5S audits and how quick it was to set up, so he decided,
“I want that for all the plants!”
Replacing the bulky, sluggish paper-based audits with Capptions was intuitive for the personnel at Ardagh, mainly because of the platform’s flexibility. Much like a set of building blocks, Capptions allowed them to build their own internal safety audit system and fine-tune it to their existing workflow.
“You are just doing a great job of listening to your voice of the customer in general. You have a lot of potential to adapt to the exact need that we have instead of having a very structured product that they need to adapt to.”
The results came very soon
Administration time was cut by four
The company consolidated all of its Excel files in a structured set of audit templates inside Capptions. Now everyone who wants to report a safety hazard or a potential improvement can do so with their smartphone, even offline. The dreaded 5S audits that used to take hours of managers’ time have been replaced with a single mobile app.
“It’s just nice that you walk, you talk to your phone or you take pictures, and then you have a full complete report that you can share with everyone. This was taking me hours before to do the same or potentially not even doing it because of lack of time.”
Now, Ardagh Group uses Capptions to manage all of its EHS challenges — from environmental safety and hygiene audits to waste identification and quality management. Everything is on one platform that can be accessed by all stakeholders. Pierre Autret says about his personal experience,
“I’m visiting a plant every other week pretty much where I’m gonna walk the plant. I’ve been able to use the app every time on this occasion and save four times the time that I use to document everything that I was doing.”
Ardagh Group’s vision is coming to life
In just two years, the Dongen plant, which piloted Capptions as an LSS tool, has seen a significant surge of reports. In the past three months alone, more than 600 new users have started using Capptions.
“I’m pleased that we have sold the product so that the plant wants it instead of the corporation pushing it and saying ‘you have to do that’. It’s a bottom-up request and, hopefully, we’ll keep it going.”
Employees can quickly identify everything that needs to be corrected, report safety concerns in the area they are in, validate standards, and easily participate in operational improvement.
“[Employees] make sure that the areas stay in the state they should and this app is validating that they do it. They follow up, they challenge each other if they don’t.
When you visit these plants, you see a lot of people, much more people, proud of their plants and their work environment.”
Ardagh Group’s vision is coming to life — everyone is becoming a process improver.
What Ardagh Group says about Capptions
Initially, the company chose Capptions as a tool to reduce the administrative burden and get EHS data from the shop floor to the back office right away. Time savings are essential but the added benefit of higher engagement has an even greater long-term ROI for the company.
“If you are still doing paper audits or any computerized format of audits, just get Capptions tomorrow because you’re gonna cut by four your administrative time and you’re gonna engage your people much more than with filing paperwork.”